The Evolution and Engineering of Rectangular Connectors
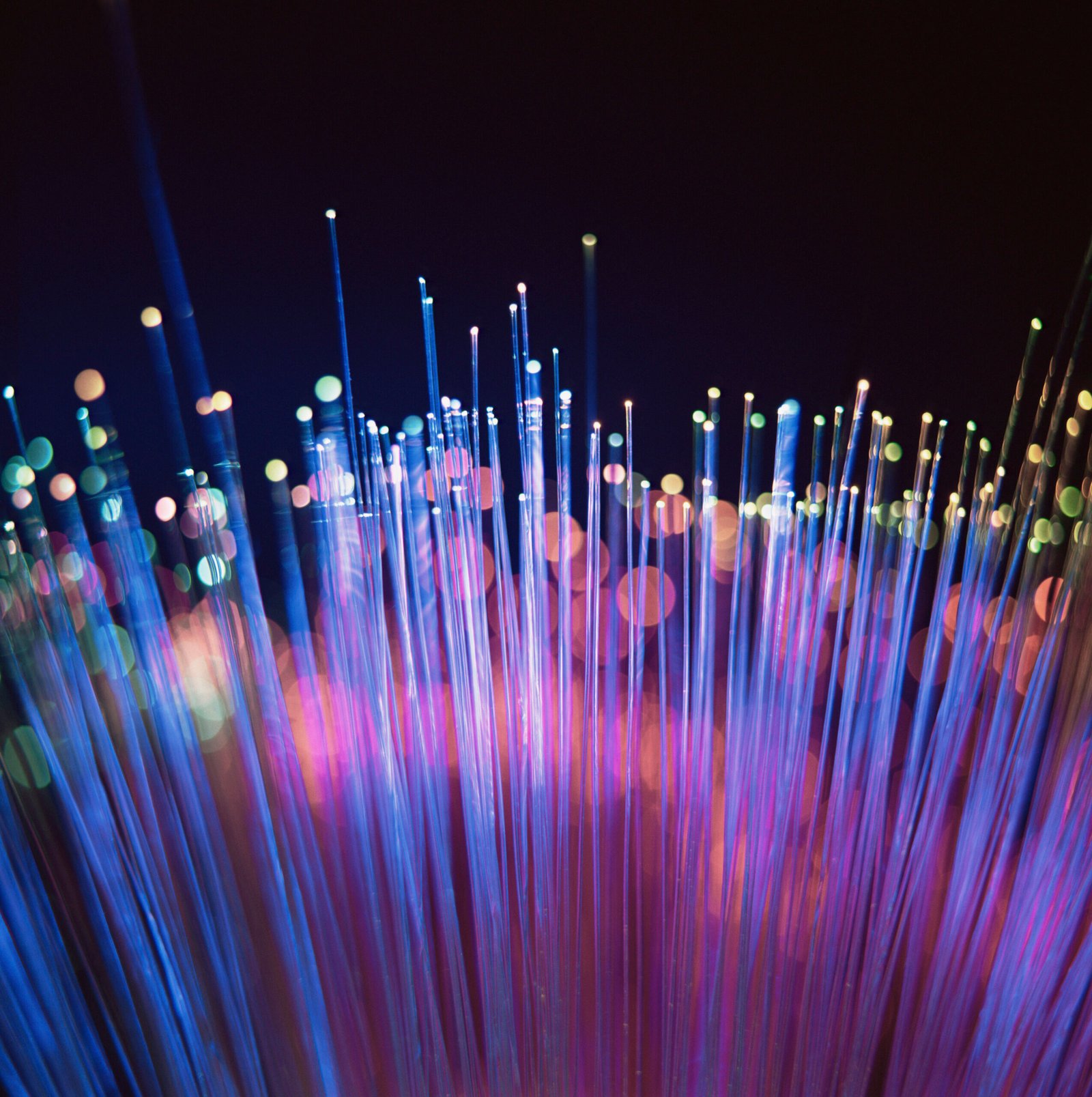
Introduction
Have you ever paused to consider the silent architects behind today’s complex electronic assemblies? Rectangular connectors—those precise, box-like junctions—form the backbone of countless systems, from data centers to defense platforms. While circular connectors often steal the spotlight with their rugged elegance, rectangular variants offer a compelling blend of density, modularity, and cost‑efficiency. Yet beneath their simple geometric silhouette lies a world of intricate engineering, standardization, and innovation. This article questions conventions and unveils the art and science of rectangular connectors, exploring their construction, applications, advantages, challenges, and future trajectory.
1. Design and Construction
Rectangular connectors might appear straightforward—two matching halves, one male, one female, aligned by guides and locked by latches. But peel back the layers and you’ll find a symphony of components working in harmony:
- Housing and Shell
Crafted from thermoplastic or metal alloys, the outer shell provides mechanical support and basic EMI shielding. Popular materials include polyphenylene sulfide (PPS) for high‑temperature tolerance and zinc die‑cast for cost‑effective robustness. - Contact Carriers and Insulators
Inside, precision‑molded insulators separate and position contacts. Contacts—typically copper alloys with gold or tin plating—are arranged in single or multiple rows, optimized for current capacity, signal integrity, or mixed power/data payloads. Insulator geometry prevents migration or deformation under thermal cycling. - Latch and Locking Mechanisms
Unlike circular connectors that rely on threaded or bayonet couplings, rectangular types use friction latches, sliding locks, or external levers. These mechanisms balance ease of mating with retention force, ensuring connections endure vibration without requiring a torque wrench. - Cable Entry and Strain Relief
Rectangular connectors integrate cable clamps or backshells that anchor cables, distribute mechanical loads, and maintain the connector’s environmental seal. Optional gaskets and potting compounds achieve IP ratings up to IP67, shielding against moisture and particulate intrusion.
In essence, every groove, ridge, and plating choice is a deliberate decision, calibrated to balance performance, cost, and manufacturability.
2. Key Applications
Why do design engineers keep reaching for rectangular connectors despite the allure of circular designs? The answer lies in their unique strengths:
- Data Centers and Telecommunications
High-density rack environments demand connectors that maximize pin counts per module. Rectangular connector modules—such as the ubiquitous RJ45 Ethernet jack or high‑speed mezzanine cards—streamline signal routing and minimize patch‑panel clutter. - Industrial Control Systems
PLCs, HMIs, and motion controllers frequently use heavy-duty rectangular connectors (e.g., Harting Han® series) for power, control I/O, and fieldbus signals. Their modular inserts allow engineers to mix power, discrete I/O, and data contacts within a single shell. - Automotive Electronics
Modern vehicles bristle with rectangular connectors: engine control units (ECUs) use multi‑pin rectangular housings for harness integrations, while infotainment and sensor modules rely on standardized rectangular interfaces to simplify assembly lines. - Consumer and Medical Devices
USB, HDMI, and DisplayPort are all rectangular connectors that have revolutionized consumer electronics. In medical imaging and diagnostics, micro rectangular connectors (e.g., D‑subminiature and micro‑rugged connectors) deliver reliable signal transmission in compact, sterilizable packages. - Aerospace and Defense
Although circular connectors dominate aerospace, rectangular rack‑and‑panel connectors (e.g., VITA VPX standard) have gained traction in ruggedized computing platforms, offering high‑speed backplane communication and hot‑swap capability.
3. Advantages Over Other Connector Types
Rectangular connectors hold several cards close to their chest:
- High Density and Scalability
Multiple rows of contacts translate to hundreds of pins in a chassis‑mount footprint. Modular insert systems allow field reconfiguration without changing the entire shell. - Cost‑Effectiveness
Thermoplastic housings and injection‑molding processes lower unit costs compared to machined circular shells. Standardized footprints reduce design iteration and tooling expenses. - Ease of Panel Integration
Flat mating surfaces simplify chassis cutouts and panel assembly. No need for threaded inserts or O‑ring grooves; rectangular connectors clip or screw directly onto PCBs or panels. - Signal Management
Internal shielding partitions and ground rails can be integrated between contact rows, minimizing crosstalk and preserving signal integrity in high‑speed digital and RF applications. - User-Friendly Mating
Visual keying and polarized housings eliminate misconnections. Latching mechanisms provide audible and tactile feedback, reducing installation errors on crowded factory floors.
4. Industry Standards and Compliance
Uniformity breeds interoperability. Rectangular connectors adhere to a suite of international standards:
- IEC 61076‑4‑101 / IEC 61076‑4‑102
Define rectangular connectors for industrial Ethernet and power over Ethernet (PoE), ensuring compatibility across vendors. - MIL‑DTL‑55302
Specifies ruggedized rectangular connectors for military avionics and ground systems, addressing shock, vibration, and corrosion resistance. - VITA 46 / VITA 48
Governs VPX and VPWR backplane connectors in embedded computing, dictating high‑speed signal lanes, power rails, and cooling provisions. - ANSI/EIA‑364
Outlines environmental testing protocols—salt spray, thermal shock, and mechanical life cycles—to validate connector endurance.
Compliance with these standards not only streamlines design cycles but also unlocks global supply chains, letting designers cherry‑pick best‑in‑class components without reinventing the wheel.
5. Design Challenges and Solutions
But don’t get lulled by the simplicity of squares and rectangles. Engineers grapple with:
- Thermal Expansion
Different materials expand at varying rates. Mismatched coefficient of thermal expansion (CTE) between housing and PCB can induce stress fractures. Solution: use compliant sockets or floating pin arrangements. - High‑Frequency Signal Integrity
As data rates climb into the multi‑gigabit realm, maintaining controlled impedance across rectangular connectors becomes critical. Many vendors now offer embedded PCB‑mated connectors with integrated ground shields and precision‑machined contact geometry. - Durability vs. Miniaturization
Shrinking pin pitch risks compromised mechanical strength. Advanced plastics—liquid crystal polymers (LCPs) and reinforced nylons—provide the necessary rigidity while allowing sub‑1 mm contact spacing. - EMI and Crosstalk
Closely packed contacts invite electromagnetic mischief. Adding internal partitions, conductive gaskets, and optional overmolds can suppress unwanted interference.
6. Future Trends
Where do rectangular connectors venture next? A few trajectories stand out:
- Ultra‑High‑Speed Modular Systems
Standards like CCIX and CXL may spawn new rectangular backplane connectors capable of terabit‑scale throughput. - Embedded Smart Connectors
Imagine contacts that self‑diagnose signal integrity, temperature, or mechanical latch status. Embedding tiny sensors could revolutionize predictive maintenance. - Sustainable Materials
Bio‑based plastics and lead‑free plating processes will reduce environmental footprints, aligning connector manufacturing with circular economy principles. - Flexible and Hybrid Interfaces
Integrating optical waveguides or soft, conformable contacts within rectangular shells could yield hybrid power/data connectors for wearable and conformal electronics.
Conclusion
Rectangular connectors may lack the romantic curves of their circular counterparts, but to dismiss them as mere “boxes” is to overlook a century of refinement in materials science, mechanical design, and signal engineering. From board‑to‑board mezzanines to ruggedized field interfaces, their modularity, density, and cost advantages make them indispensable in modern electronics. As data rates soar and form factors shrink, rectangular connectors will continue to adapt—ever questioning, ever innovating—ensuring that our electronic architectures remain reliable, scalable, and ready for the next frontier.