The Intricacies of Connector Contacts
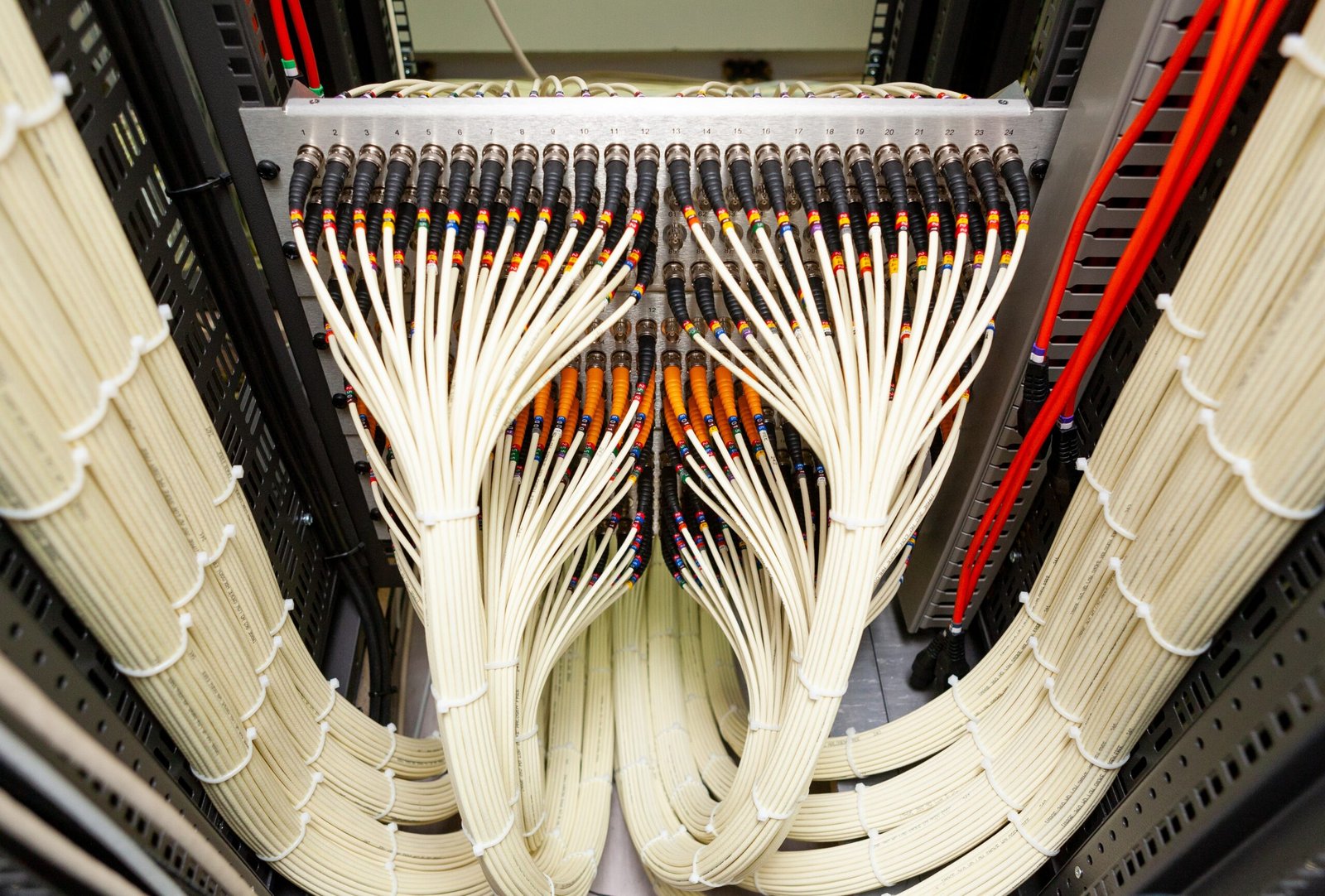
Introduction
Connector contacts are the unsung heroes of every electrical and electronic system. They form the critical interface through which power, signals, and data traverse from one component to another. Despite their diminutive size—often mere millimeters in length—contacts dictate overall system reliability, performance, and longevity. In this article, we delve into the design, materials, types, performance metrics, challenges, and future trends surrounding connector contacts.
1. Fundamental Role of Contacts
At its core, a connector contact serves two primary functions: to provide a low-resistance electrical path between two conductors, and to maintain that path under mechanical, thermal, and environmental stress. Poorly designed or degraded contacts can introduce voltage drops, generate heat, or even fail completely, leading to system malfunctions. Thus, understanding contact behavior is essential for engineers across industries—from consumer electronics to aerospace.
2. Contact Materials and Plating
Materials selection lies at the heart of contact performance. The most common substrates include brass, phosphor bronze, and beryllium copper. Each alloy offers a unique balance of conductivity, strength, and resilience to fatigue. To enhance surface properties, contacts undergo plating with noble or semi-noble metals:
- Gold: Provides excellent corrosion resistance and stable low contact resistance. Ideal for low-current, high-reliability applications such as medical implants and precision instrumentation.
- Silver: Offers superior conductivity but is prone to tarnishing. Silver plating is common in high-current power connectors and RF applications, where minimal resistive losses are critical.
- Tin: Economical and solderable, tin plating suits mass-market electronics. However, tin can form whiskers over time, posing a risk of short circuits in high-reliability contexts.
- Palladium and Nickel: Often used as underlayers or in multi-layer stacks to buffer between the base alloy and the outer noble layer, preventing intermetallic diffusion and preserving contact integrity.
3. Contact Geometry and Mechanisms
Connector contacts rely on mechanical design to ensure consistent mating force, wiping action, and retention:
- Leaf Springs and Beam Contacts: Flexible metal springs apply a continuous force against a mating pin or blade. The degree of deflection and the spring’s shape determine contact force, insertion force, and mechanical wear.
- Box and Socket Contacts: Box (female) contacts surround a male tab or blade. Their geometry offers robust retention and dual wiping surfaces, improving contact cleaning during mating cycles.
- Pin and Receptacle Contacts: Common in circular and rectangular connectors, pins insert into precisely aligned receptacles. Concentric or dual-spring receptacle designs can enhance reliability under vibration.
- Edge Card Contacts: Found on PCB cards, these contacts ride along conductive pads, using wiping action to remove surface films. Their design supports thousands of mating cycles in card-edge connectors.
4. Performance Metrics
Quantifying contact quality involves several key parameters:
- Contact Resistance: Measured in milliohms (mΩ), this reflects the resistance across the mated interface. Lower resistance translates to reduced I²R losses and heat generation.
- Insertion and Extraction Forces: Expressed in newtons (N), these forces dictate user experience and connector life. Designers strike a balance: high enough to ensure retention, but low enough for ergonomic mating.
- Wiping Action: The relative sliding motion between contacts during mating scrubs away oxidation or contaminants. Contacts designed with deliberate offset angles optimize this self-cleaning effect.
- Mating Cycles Durability: Specified as the number of connect/disconnect operations a contact can endure before performance degrades beyond specification. High-reliability connectors may guarantee upwards of 10,000 cycles.
5. Environmental and Reliability Considerations
Contacts must operate flawlessly across varied conditions:
- Temperature Extremes: Thermal expansion and contraction can affect contact pressure. High-temperature alloys and compliant spring designs maintain consistent performance from −55 °C to +150 °C.
- Corrosion and Contamination: In outdoor or industrial settings, contacts face moisture, dust, and chemical vapors. Sealed connector housings, contact protection caps, and corrosion-resistant platings mitigate these threats.
- Vibration and Shock: In automotive, aerospace, and military applications, mechanical shocks and continual vibration challenge contact stability. Double-spring or molecular spring contacts provide redundant contact points to withstand such stresses.
6. Specialized Contact Types
Innovation has given rise to specialized contacts tailored for unique demands:
- Fiber Optic Hybrid Contacts: Combine electrical contacts with fiber-optic ferrules in one housing, enabling simultaneous power and optical data transmission for sensing and communication systems.
- High-Speed Differential Pairs: For USB, HDMI, and Ethernet, twin contacts maintain precise spacing and impedance control, minimizing crosstalk and preserving signal integrity at gigabit rates.
- Power Blade and Busbar Contacts: Flat, broad surfaces reduce resistive heating in high-current applications such as EV charging stations and industrial power distribution blocks.
- MEMS-Based Microcontacts: Leveraging microelectromechanical systems, these contacts operate at sub-millimeter scales, enabling ultra-miniaturized wearable devices and implantable electronics.
7. Common Challenges
Despite meticulous design, contacts face persistent obstacles:
- Wear and Fretting Corrosion: Microscopic movements under load generate debris and oxidation at the interface. Self-lubricating coatings and controlled wipe distances can reduce wear.
- Material Mismatch: Dissimilar metals can form galvanic couples, accelerating corrosion. Engineers often specify compatible plating stacks or introduce insulating layers to interrupt galvanic paths.
- Whisker Growth: Particularly with tin platings, metal whiskers can emerge over years, risking shorts. RoHS-compliant tin-silver-copper alloys and conformal coatings help suppress whisker formation.
- Contact Resistance Drift: Over time or through thermal cycling, resistance can increase, impacting power delivery. Continuous monitoring and predictive maintenance schemes are increasingly adopted to catch drift before failure.
8. Quality Assurance and Testing
Ensuring contact reliability demands rigorous testing:
- Electrical Endurance Testing: Repeated mating cycles under load, measuring resistance after every set of cycles to detect degradation.
- Environmental Stress Screening (ESS): Exposing connectors to thermal shock, humidity, and salt spray per standards like IEC 60068 and MIL-STD-202.
- Mechanical Life Evaluation: Subjecting contacts to vibration profiles and shock pulses to validate retention and integrity.
- In-situ Monitoring: Embedding sensors in high-value or critical applications to track contact temperature and resistance in real time, facilitating proactive maintenance.
9. Future Directions
The evolution of connector contacts continues, propelled by emerging needs:
- Smart Contacts: Integrating micro-sensors and ICs within the contact assembly to report wear, temperature, and connection status to system controllers.
- Additive Manufacturing: 3D printing metallic contacts with complex internal channels for cooling or self-lubricating reservoirs, impossible via traditional stamping.
- Graphene and Novel Coatings: Leveraging two-dimensional materials to create ultra-thin, wear-resistant, and conductive contact layers that resist corrosion without heavy precious-metal plating.
- Liquid Metal Contacts: Research into low-melting-point alloys (e.g., gallium-based) promises self-healing interfaces and ultra-low resistance, though challenges remain in containment and reliability.
Conclusion
Connector contacts may be small, but their impact on system performance is immense. By mastering materials science, precision mechanics, and environmental protection, engineers ensure that these tiny elements deliver power and information reliably, even under the harshest conditions. As we push toward higher data rates, denser packaging, and smarter systems, connector contacts will continue to evolve—ever more sophisticated, ever more vital in weaving together the electrical tapestry of modern technology.